Inventory Management Software Development [Case Study]
![Inventory Management Software Development [Case Study]](https://cdn.prod.website-files.com/6596cfe3248a187c3480f26d/65bcb987eef9cf1d08484315_22.webp)
The past few years have heralded a notable increase in the acceptance of new, cutting-edge inventory management solutions. The pivotal factors in this surge include the fast rise in e-commerce popularity, demand for RFID technology, widespread adoption of smartphones and other mobile devices, and the need to reduce supply chain inefficiencies. These have effectively taken down the reluctance of most businesses to switch from legacy systems and invest in inventory management software development.
Therefore, the market, which was at 3 Billion (USD) in 2019, is expected to grow at a CAGR of over 5% between 2020 and 2025, reaching 5 Billion (USD) according to Global Market Insights.
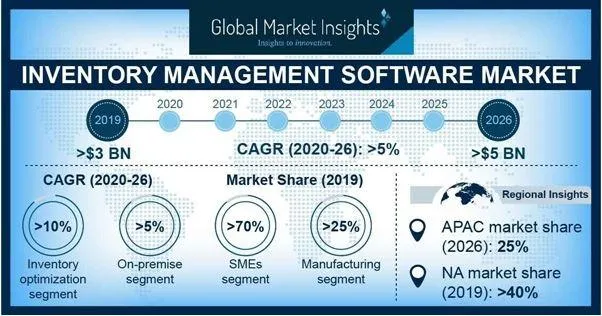
Source: Global Market Insights
Impressively, it would be no surprise if these numbers are surpassed as the demand for robust software to improve and control the supply chain across the e-commerce and manufacturing sectors is predicted to further fuel the market demand. So, to stay competitive and efficient, companies are now looking to create inventory management software with the help of development companies like Appvales, boasting an excellent track record building MVPs for both start-ups and large enterprise systems.
That being said, the development process focuses on ensuring the product enables the seamless, efficient tracking of inventory levels, orders, sales, and deliveries. In addition, It can also create work orders, bills of materials, and other production-related documents in the manufacturing industry. However, every software is unique depending on one’s needs. Therefore, to help you communicate effectively with the development team on what you expect, here are some core features that you should consider for your project.
Core features of Inventory Management Software
When starting an inventory management software project, one must inform the development team of the features they need to integrate into their system. These features will determine the solution’s ease of use, efficiency, and productivity, hence, the importance of knowing them and selecting which to include. The most common inventory management system software features include:
Reorder Point
Stock management software provides the user a product list and the required stock quantities. When the quantities reach a certain pre-programmed point, the software immediately alerts the manager to reorder a predetermined amount of the product. Therefore, the shortage of and excess stocking is prevented.
Asset Tracking
With this stock management feature, one can use radio frequency identification, barcodes, serial or lot tracking numbers to track their warehouse or store products.
Product Listing
With this feature, one can systematically keep their items by creating each item’s alternative based on its principal attributes. In addition, the feature permits the user to organize their inventory, using essential details like availability, cost, SKUs, and so on. Therefore, this is one feature highly recommended to include in inventory software development.
Barcode Scanning
This inventory tracking software makes use of product barcodes to keep track of them. To eliminate the need for expensive scanning hardware, smartphones can be employed in the exchange of electronic data.
Reporting Tools
Many reporting tools are used to develop inventory management systems’ order history, transaction reports, and total reports. When included in the inventory management software development, these tools let the user create a smooth workflow by providing information on a stock that needs re-ordering, is profitable, and more.
Inventory Forecasting
To avoid having too much or too little stock, one has to decide how much to buy. This feature makes the decision process easier by forecasting how much your type and size of the company would need to purchase. Therefore, one makes the right decisions and protects their productivity and sales.
Inventory Alerts
When inventory levels drop below the user’s preset threshold, alerts are created and sent to them via SMS or emails. This way, one knows when it’s time to restock in advance.
Accounting Tools
Overhead allocation, cost layering, disclosures, measurements, and more are accounting tools that aid the derivation of a more precise evaluation of stock. This tool removes the struggle of manual evaluation, thereby saving time and money while being more efficient.
Raw Material Tracking
This is used in deciding when there are adequate raw materials for more or new jobs in production. Therefore, one can more reliably determine more productive alternatives for the workforce to focus on. Labor costs are also kept in check with this tool.
Inventory Levels for Parts and Finished Products
This ensures the user knows what is readily available and ready for purchase and instant delivery to the client. These could be finished products in the warehouse or in the store.
Automatic Re-ordering
With this feature, reordering stock is automatically done once the minimum limit is reached, ensuring you’re always on top of your inventory.
Integrations with ERP or Maintenance Software
Re-entering information in separate programs can be cumbersome. Therefore, making sure developers integrate with ERP or maintenance software during inventory management software development is critical to the seamless flow of data.
Multiple Location Support
A tool vital for companies with multiple locations that ensures data across all sites is compiled and tracked in one system. This way, one can keep track of the total business stock effectively.
Shelf and Bin Tracking
Managers must know where a particular item is located in the warehouse for access without delay hence the need for this feature. For a personalized experience, your specifications determine the inventory tracking system design.
Order picking support
This feature helps put the customer’s order together in the required quantities before shipment.
Real-time Inventory Tracking
With this feature, one can track their inventory anywhere it might be in real-time.
Serial Number Tracking
From the moment an item is received and its serial number recorded in the system, it can be tracked until it is released. When a product is returned, its serial number in the system can be used for verification.
Expiration Date Tracking
This feature allows one to know the expiry dates of products in the warehouse or store. Therefore, one can plan informed which products have upcoming expiry dates.
Item Images
With this, you can assign multiple images to an item in the warehouse or set one image for quick reference.
Price/ Cost List
This feature allows you to pre-set price levels to items that you can easily quote to customers.
Logistics
A third-party logistics feature brings transparency to inventory logistics. This includes trackers and transport analytics which provide users and managers with location and estimated time of arrival information.
Inventory Management Trends:
There are top trends not to miss when one endeavor to create inventory management software that stands the test of time and maximizes on the latest technological advancements. Here are the current top trends in inventory management software development:
Going mobile
A company that integrates mobility into their inventory management software project will:
- Enhance visibility of all the processes on all levels.
- Get real-time inventory management.
- Reduce cycle counts and physical inventory times.
- Monitor all procedures effortlessly.
AI and machine learning
The value of artificial intelligence and machine learning in inventory software development cannot be emphasized enough. This is because AI in inventory management enhances process optimization, gathering insights, and making informed decisions. This allows for demand forecasting, cost optimization, maintenance scheduling, and, most importantly, intelligent decision-making.
Computer vision
This technology allows a computer or machine to read and interpret image and video information. Some of the applications of computer vision inventory management include:
- Barcode and text label scanning.
- Labeling, tracking, and tracing.
- Packaging inspection.
Due to its application in these management areas, CV benefits the user through:
- Stocktaking improvement
- Human error mitigation.
- Increase in productivity, and more.
Blockchain
Those who have been following banking, investing, or cryptocurrency over the last ten years may have heard the term “blockchain.” This is a specific type of database that differs from a typical one in how it stores information. Blockchains store data in blocks that are subsequently chained together. The use of this technology in inventory management is forecasted to rise to 54% over the next five years from a meager 5% recorded in 2018.
Drones
Drone inventory management might sound a bit far-fetched. However, it shouldn’t in a world where companies like Google and Amazon deliver products to customers via drones. These devices are taking off in the logistics sector, serving as support for stock management and other tasks. For example, warehouse drones are fast becoming game changers in taking annual inventory, which usually involves stopping all or part of the facility’s activity so that operators can scan all of the items. Drones could free workers from tedious jobs in this operation and enable the warehouse to continue operating normally.
In addition, the use of warehouse drones in manual inventories essentially puts an end to human error and inefficiencies. Drones independently fly around the facility, scanning barcodes, and RFID tags while informing the WMS of their findings and progress.
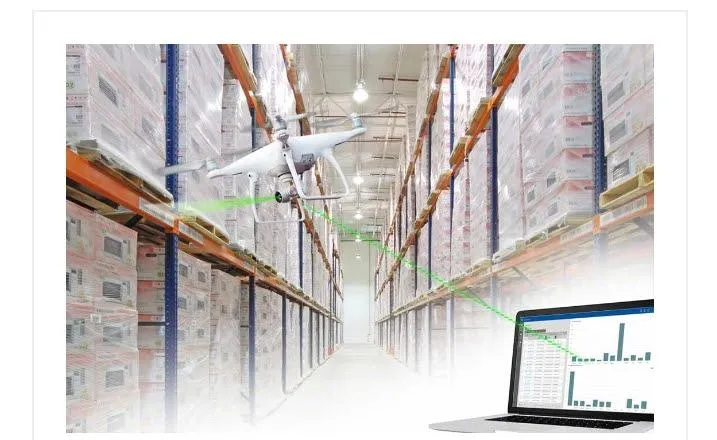
Therefore, drone use can be beneficial for automatically avoiding stock mismatches and ensuring that warehouse activity continues as usual while taking annual or periodic inventory.
Going to cloud
Cloud-based inventory management systems can be accessed from all types of devices. Also, this inventory management system software is IoT-driven, making it easier to record all the inventory details intelligently and smartly. IoT keeps the inventory optimized and efficiently organized as all relevant company employees get real-time updates on a wide range of devices. A significant cloud computing advantage is information storage for ease of access and loss protection.
How to Build Inventory Management Software
To create inventory management software, there are steps that you have to go through to ensure everything goes as planned. Two steps come before hiring the development team and two more after. None of these is any less than the other and should be followed religiously. The steps are:
- Write the requirements and user stories.
Approaching a software development team before you know what you require of them and without proper user stories is a waste of time. In addition, the requirements and user stories have to be given in the right way.
Requirements:
Since there will be changes during the development process, giving, too detailed and concrete requirements is impossible. Instead, the service, function, or feature you need should be stated in a way that leaves room for flexibility without tying these specifications to a solution. Therefore, mentioning the desired achievement without stating how to achieve it is the optimum way of giving requirements. For instance, ‘a flight method’ instead of saying ‘a helicopter’ gives the developers more room to create inventory management software that caters to your needs. Note that to cover all bases, your set of requirements must mention both the functional and non-functional features of the solution.
User stories:
Also known as Epics, user stories for inventory management system are requirements stated from the end-user goal context. Epics are meant to facilitate communication between the client and the developer by expressing requirements more understandably.
- Plan time and budget.
Reasonable time estimates based on past projects with similar requirements are essential. However, always remember that meticulous application development takes time. As such, patience is vital in the development process. In addition, create a budget to cover the creation of management software that will stand the test of time.
- Hire a development team or outsource
Depending on your timeframe, budget, and other factors, you could choose to either hire a development team or outsource. However, fully employing a team of developers would require a long process with HR accepting applications, interviewing, and testing potential employees. This would not be time and cost-effective and also draws your focus from the main drive of your company. Therefore, hiring a team that is already familiar with each other and knows how to create an inventory system is advised. Outsourcing is another effective way to get this done without all the hustle of employing in-house developers.
- Test the system.
Once the team is done, the system should not be hurried to full use without testing. This helps you familiarize yourself with the software and is essential to see if it functions expectedly and if all features you required were included.
- Maintain.
Including a maintenance agreement in the development project is vital. It ensures you will not experience severe drawbacks if the system needs a fix, an upgrade, or even an overhaul, depending on your maintenance agreement terms.
Inventory Management Software Development Cost
No inventory management software project is the same. Therefore, to get an accurate quote, the developers need to have all the precise requirements first. However, the average cost of the inventory management system is an estimated $30K – $50K for an MVP, while a full-featured version should cost you no less than $100K.
How We Built Store Management Web Application for a Client
We made a flawless Tobacco control and reports system for our client. In this section, we shall go into detail on how to create an inventory system in python.
- Problem + timeframe
USA governmental institutions and private agencies needed a store management web application for tobacco control and reports. Building this system took about two weeks in the engagement process phase and two for the formal commitment to proceed. The formal commencement of the project, including the design specification, solution documentation; prototype; and system test plan and cases, took three months, while the post-launch commencement period was two weeks. We then started the formal maintenance and support agreement as required of us by the client. Therefore the whole project was done in less than five months.
- Features, User stories
The features included were asset tracking, multiple location support, real-time inventory tracking, reorder point, product listing, to name a few. In addition, the detailed yet precise user stories were vital in developing a system with all client requirements.
- Solution + tech stack
Finally, the solution delivered was a high quality, efficient system built by a dedicated software development team using the following stack:
Technological stack:
The store management application development saw Appvales using different technologies, including:
- Python
- Django
- React
- Redux
- Celery
- Redis/RabbitMQ
The Back-end developers developed the stock management application using Python as the development language. First, the API Framework was done using the Django REST Framework. Then the Database was created by Postgres + PostGIS. Finally, for Background task processing (geoprocessing, import process, etc.), Celery + Redis/RabbitMQ were used.
The Front-end developers used JavaScript as the development language. The framework was created using React + Redux. DevOps: AWS: EC2 – as API and front-end instance; RDS – database storage, S3 – file storage.
The Application was also dockerized to deploy and run any app on any infrastructure quickly and reliably.